Эффективное управление запасами предприятия
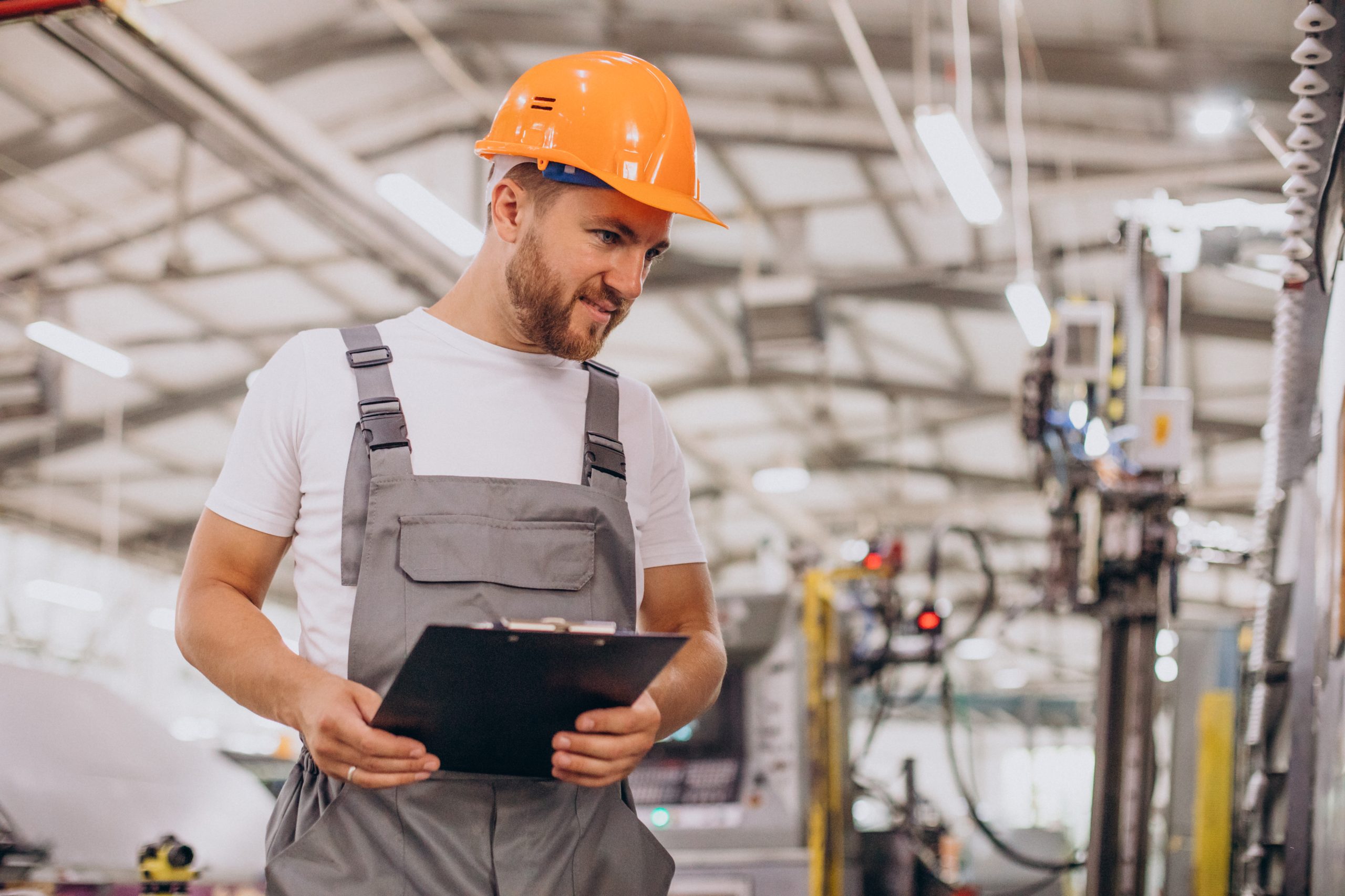
Содержание статьи:
- Принципы эффективного управления запасами предприятия
- Эффективное управление запасами предприятия в разных моделях
- Модель 1. Склад завода – как место хранения. Система «выталкивания»
- Модель 2. Склад завода – это буфер в цепи поставок. Система «вытягивания»
- Как организовать эффективное управление запасами: выводы
Принципы эффективного управления запасами предприятия
Эффективное управление запасами — основа стабильного бизнеса. Сегодня расскажем подробно про важность наличия склада, и про главные принципы управления запасами на складе, их плюсы и минусы. Также ответим на вопросы: Для чего необходим склад? Какое влияние оказывает наличие склада на эффективное управление запасами предприятия?
На первый взгляд, все просто: склад – это место, где хранится товар, который мы используем в продажах. Но существует два принципа управления запасами на складе. Подробнее:
- Принцип «выталкивания»
Анализируя продажи предыдущего периода, составляется прогноз на будущий период. Продукт производят или заказывают согласно прогнозу, и размещают на складе. Если прогноз не свершился, возникает вопрос: Что делать с избытками или недостатками запасов? Таким образом, управление запасами на производстве на основе прогноза — неэффективно и порождает проблемы в бизнесе. - Принцип «вытягивания»
Продукты создают на основе фактического спроса, а не прогнозов. Благодаря этому, компания не имеет «упущенных продаж» и имеет возможность сосредоточиться на эффективном использовании своих ресурсов, а также уменьшения вероятности перепроизводства. Но есть и слабая сторона данного принципа. В случае глобальных изменений или появления новых SKU, у предприятия появляется необходимость в дальнейшем прогнозе, поскольку спрос на глобальном уровне не сработает.
Ниже рассмотрим, как работают обе системы на примере предприятия.
Эффективное управление запасами предприятия в разных моделях
Модель 1. Склад завода – как место хранения. Система «выталкивания»
Так как спрос на 50 SKU колеблется, и угадать его невозможно, по некоторым запасам товара возникают нулевые остатки, а остальные товары – в избытке. Потребитель не знает о наших прогнозах. В конце месяца у дистрибьюторов возникает разная потребность на эти 50 SKU, которая не совпадает с ранее размещенным заказом на следующий месяц.
В итоге, компания получит товар, который сейчас не нужен, а который ранее заказала, но не угадала с прогнозом. Возникает вопрос: что делать с «ненужным», но заказанным товаром? Есть два варианта: получать и продавать товар со скидкой, или размещать на своих складах. Размер партии «ненужных» товаров в нашем случае – это 1 месяц продаж.

Хочу обратить внимание на то, что завод произвел «ненужный» товар, и тем самым неэффективно использовал свои производственные мощности. Казалось бы все нормально: продукцию отгрузят, обязательство в деньгах возникнет. Но мы знаем, насколько проблематично забирать у партнера задолженности за товар, который не был им реализован. Отгружать новые партии продукции сложно из-за того, что появилась дебиторская задолженность за «ненужный» товар. Это усложняет взаимоотношения с партнерами и снижает эффективность управления запасами предприятия.
Давайте предложим систему управления запасами, основанную не на долгосрочном прогнозе. При этом нам необходимо перестроить некоторые процессы для сокращения времени реакции на запрос клиента.
Модель 2. Склад завода – это буфер в цепи поставок. Система «вытягивания»
Пример 2. На складе завода, на основе спроса 20 дистрибьюторов рассчитывают и создают целевые уровни запасов (в днях). Данные уровни учитывают время производства и минимальную производственную партию продукции для каждого SKU.
В ассортиментной линейке 50 продуктов: из них, — около 10 продуктов – быстро продаваемые, следующие 10 – медленно продаваемые или неходовые, но их необходимо держать для ассортимента, а более 30 – средне продаваемые. Это означает, что уровень запасов различных SKU — разный.

Согласно потребностям, партнеры забирают со склада товар, на два-три дня. Завод видит фактическую отгрузку со своего склада, и уже имеет четкую производственную программу. Программа разложена по приоритетам, чего нет в случае с первым складом, когда срочная потребность возникает у всех 20 дистрибьюторов по 50 SKU, в связи с неравномерным спросом и несоответствием продаж и прогноза.
То, что было отгружено в большем количестве, имеет более высокий приоритет выполнения на производстве. Размер партии определяется согласно отгруженному количеству товара с учетом потребления: если потребление нарастает, — увеличивается уровень запасов на складе, а также размер заказа для производства, и, наоборот, если потребление падает, – уровень запасов и размер заказа сокращается. При этом размер партии не может быть меньше определенной минимальной партии производства.
В связи с тем, что количество быстро оборачиваемых продуктов небольшое, а у нас есть страховой запас на средне оборачиваемые и низко оборачиваемые продукты, мы имеем возможность, используя приоритеты, поддерживать необходимый уровень запасов для всего ассортимента, при этом сокращая время производства, время реакции на спрос и уровень запасов.
Выпуск по приоритетам похож на работу профессионального жонглера в цирке. Булав, которые он подбрасывает, много, но они идут в четком приоритете и последовательности, и, фактически, они все в «работе» в воздухе, несмотря на то, что производительность ограничена только двумя руками жонглера.
Имея в наличии на складе нужный ассортимент, компания получает увеличение спроса на продукцию, что ведет к более высоким продажам и большей прибыли. Существует единственная проблема – преодолеть барьер в количестве переналадок. Для решения проблемы необходимо понять минимальную партию продукции для производства, и начинать производство по достижению размера заказа со склада до уровня минимальной партии.
Больше про эффективное управление запасами с методологией Demand Driven MRP
Как организовать эффективное управление запасами: выводы
Две концепции использования склада имеют разное влияние и результат на эффективное управление запасами предприятия. В системе «выталкивания» компания использует склад для переработки груза, а в системе «вытягивания» – компания защищает свои продажи.
В концепции «вытягивания» компания получает четкие приоритеты для работы производства, и поэтому в состоянии сократить время реакции на спрос, что, в свою очередь, уменьшает уровень запасов в системе.
Убедиться в том, что большинство компаний использует склад — как помещение для хранения, просто: зайдите в супермаркет и оцените наличие товара на полках. Несмотря на то, что некоторые компании придают большое значение поставкам и штрафуют поставщиков за отсутствие необходимого ассортимента, товар все равно «выпадает». Это говорит о том, что производство не в состоянии на 100% обеспечить клиентов.
В производстве и дистрибуции для управления запасами предприятия успешно применяется методология DDMRP (Demand Driven Material Requirements Planning) — планирование потребности в сырье и материалах на основе фактического потребления и управление запасами готовой продукции.
В следующих статьях мы напишем о том, как автоматизировать управление запасами на производстве по методологии Demand Driven MRP. Прочитать о системе управления запасами Intuiflow вы можете здесь.