Управління виробничими запасами в будівельній індустрії: Вдосконалення від гігантів галузі
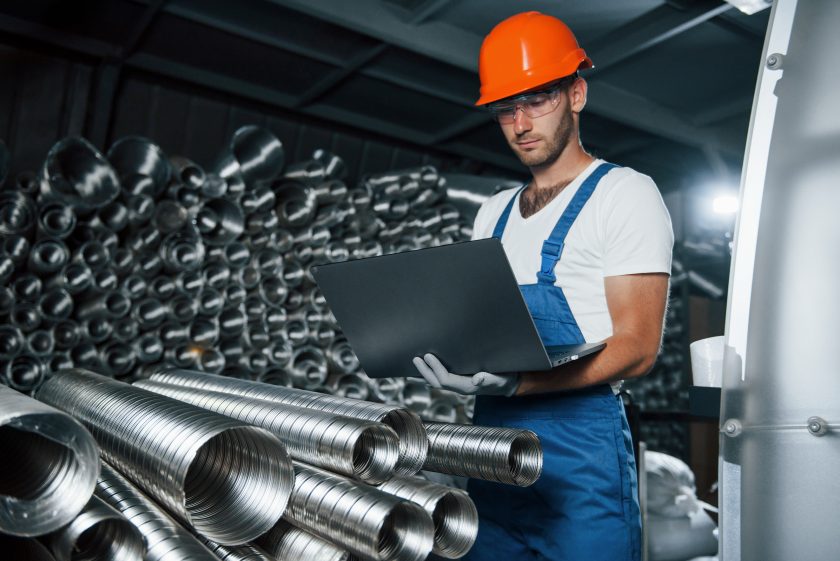
Управління виробничими запасами та ланцюгами постачання в будівельній галузі – це важке завдання. Висока сезонність, нестабільний попит, складна логістика та багатоступінчаті ланцюги постачання – це лише декілька з проблем, які стоять перед керівництвом будівельних компаній.
Розповідь про один із таких випадків – про клієнта, який зіткнувся з непростими завданнями управління запасами, може кинути світло на те, як він вирішив свої труднощі та досяг успіху завдяки впровадженню нових стратегій та технологій. Давайте розглянемо, як це сталося.
Якими особливостями вирізнялось управління виробничими запасами у компанії-клієнта?
На момент знайомства з клієнтом ми відзначили, що компанія має стабільне становище на ринку та великий потенціал розвитку при унікальному обладнанні, а також професійну команду менеджменту, яка прагне інновацій.
Проте, виникло питання: чи відповідає поточна система управління ланцюгами постачань амбітним цілям компанії? Для з’ясування цього перед початком проєкту була проведена діагностика.
Чим же характеризувалося планування запасів на момент передпроєктного обстеження:
-
Складні багаторівневі ланцюги постачань,
За участі більше двох внутрішніх складів, та двосторонні товарні потоки. Це вимагає взаємодії між філіями компанії, як постачальниками та покупцями різних продуктів.
-
Яскраво виражена сезонність
Призводить до суттєвих коливань попиту та змін у строках логістики і виробництва, що вимагає необхідності накопичувати та напрацьовувати обсяги для сезонних продажів заздалегідь для рівномірного навантаження виробничих потужностей протягом року.
-
Планування виробництва та закупівель базувалося на прогнозі продажів
Який був не точним, не часто коригувався. Цей нерегулярний процес змін призводив до завищених запасів та зменшення рівня сервісу.
-
Планування поповнення запасів велося вручну
За допомогою Excel без інструмента автозамовлення та системи індикації критичних ситуацій. Це призводило до зайвих зусиль співробітників та підвищеної ймовірності помилок.
-
План виробництва продукції, що зберігається, мав фіксований горизонт планування на місяць
Відсутність гнучкості у зміні плану призводила до низької реактивності на зміни поточного попиту.
-
Базові логістичні параметри та інші дані, необхідні для планування поповнення запасів, були неповні та неактуальні
Аналіз застарілих або помилкових замовлень спричиняв проблеми при оцінці актуального попиту.
Всі перелічені особливості, MRP-підхід в управлінні виробничими запасами та слабка автоматизація процесу призводили до бімодального розподілу запасів, неоптимальної їх вартості та оборотності, а також низького рівня обслуговування клієнтів, та збільшеної трудомісткості управління запасами.
Щоб вирішити ці проблеми та покращити систему управління виробничими запасами, керівництво компанії почало впровадження методології DDMRP та SaaS рішення INTUIFLOW.
Детальніше про бізнес клієнта
Це сфера будівельної галузі та виробництва металевих матеріалів.
- Компанія налічує понад 15 виробничих комплексів та більше 50 торгових підрозділів
- Більше 50 000 постійних клієнтів
- Асортимент налічує 100+ власних брендів
- Понад 4000 відвантажень клієнтам щодня
Діапазон діяльності компанії охоплює приватне будівництво, комерційні та громадські об’єкти, спортивні споруди, виробничі комплекси, торгово-розважальні центри.
Високий рівень лідерства компанії досягається завдяки:
- Використанню передового обладнання та технологій.
- Впровадженню сучасних підходів до організації внутрішніх бізнес-процесів, зокрема управлінням поповненням запасів.
Перед впровадженням технологій, компанія інвестувала в навчання з методології DDMRP для своїх працівників з різних підрозділів, включаючи топ-менеджмент. Це створило основу для успішного впровадження принципів методології та системи Intuiflow.
Які філії для автоматизації обрали та чому?
Проєкт впровадження було розпочато з однієї з чотирьох великих філій, яка включає два виробничих майданчики та 18 торгових підрозділів з керованим асортиментом понад 7000 SKU. Під час роботи з цією частиною ланцюга постачання було покрито два рівні поповнення – регіональний склад з власним виробництвом та торгові підрозділи, які отримують від них товари.
Вибір саме цієї філії був обумовлений декількома чинниками:
- Великий регіон, що включає виробничі та розподільчі об’єкти.
- Специфічні особливості філії, а саме, кліматичні та логістичні умови (відстань до центрального складу, довгі терміни постачань, дорожні обмеження протягом певних місяців). Логіка цього рішення була наступна – якщо методологія впорається з цими обмеженнями, масштабування на інші регіони буде просто питанням часу.
- Зацікавленість команди фахівців у покращенні показників ефективності та відкритість до інновацій.
- Різноманітність складської програми (різна продукція, яка потребує буферизації).
Цілі компанії перед реалізацією проєкту по управлінню виробничими запасами:
- Оптимізувати запаси компанії при одночасному збільшенні рівня сервісу, і прискоренні оборотності.
- Автоматизувати процес поповнення (закупівлі, переміщення, виробництво) для усунення несистемності в управлінні запасами, мінімізації людського фактору, спрощення і полегшення праці співробітників.
- Побудувати прозору систему управління ланцюгом постачань у межах обраного пілота, на основі принципів методології DDMRP
Кількісні ефекти від використання системи
1. Зміни в структурі запасів
За період використання системи відбулися істотні поліпшення в структурі запасів торгових підрозділів:
- кількість критичних SKU, за якими є ризик дефіциту, скоротилася в 3 рази.
- кількість позицій із зайвим запасом, питома вага яких займала близько 60% у структурі запасів, знизилася на 35%.
- частка SKU в оптимальному стані (зелений пріоритет) зросла з 15% до 46% (майже в 3 рази).
Структура запасу стала більш “здоровою”, безпечною і збалансованою. Відбувся закономірний зсув від бімодального розподілу.

Динаміка надлишків у грошовому виразі
2. Зростання рівня сервісу на 5% при одночасному зниженні залишку на 22%
Скорочення запасів відбувалося поступово з моменту початку роботи в системі, під час сезону (зниження на 24%), і в період виходу з нього.
За рік впровадження INTUIFLOW той самий рівень продажів, що і минулого року (різниця 5%) був забезпечений рівнем запасів на 36% меншим, ніж в рік до використання системи.
Рівень сервісу у філії став одним із найвищих в компанії порівняно з іншими регіонами та показав одну з найкращих динамік за рік (+5%).
3. Прискорення оборотності в днях на 35%
До початку проєкту оборотність у днях на розглянутій філії поступалася середнім значенням по компанії. Однак за рік впровадження Intuiflow показник став найкращим серед інших регіонів і показав успішну динаміку (максимальне зниження на 35%). У тому числі за рахунок цієї тенденції покращився і середній показник по холдингу загалом.

Візуалізація ефектів від використання Saas рішення INTUIFLOW
Якісні ефекти від використання системи
Під час проєкту було досягнуто й істотних якісних поліпшень, які складно оцифрувати, проте їхній вплив відчутний як на щоденну роботу менеджерів, так і на кінцеві економічні ефекти.
Чистка асортиментних матриць
Це перший крок, з якого необхідно почати, адже підтримання в постійній наявності позицій, необгрунтованих з погляду попиту, загрожує заморожуванням обігових коштів у неліквідах і нераціональним використанням площ для зберігання.
Список активної номенклатури був переглянутий з точки зору затребуваності на конкретному складі, обсягу і частоти продажів, кількості клієнтів, які замовляють його протягом року.
Вибір позицій, які доцільно підтримувати в постійній наявності на даному місці зберігання – це стратегічне рішення, від якого залежить повернення на інвестиції в компанії.
У результаті цих дій поточні матриці були оптимізовані й точніше стали відображати потребу торгових підрозділів. Кількість позицій було скорочено на 14%.
Прозорість в управлінні виробничими запасами. Весь ланцюг постачань як на долоні.
Оскільки і Регіональний склад і торгові підрозділи, які він забезпечує, під’єднані до системи, можна швидко і комплексно оцінити ситуацію з будь якою SKU по всій мережі. Де вона в дефіциті та її потрібно поповнити, а де в надлишку.
Також система фокусує увагу менеджера тільки на відхиленнях і проблемних зонах. Завдяки розстановці пріоритетів поповнення, менеджеру не потрібно аналізувати всі позиції, система зверне увагу на необхідні.
Оскільки до впровадження системи менеджери не мали достатньо часу для перегляду всіх позицій, значна їхня частина втрачалась з фокусу і замовлялась пізно, коли вже наставав дефіцит. А це означає, щонайменше впродовж lead time товару не було на залишку, що погіршувало рівень сервісу за клієнтськими замовленнями. І навпаки, деякі позиції, які не потребують замовлення, піддавалися аналізу і витрачали цінний час.
Система пріоритетів і сповіщень дала змогу:
- підвищити рівень наявності запасів
- знизити кількість додаткових замовлень, які створювали у разі відсутності товару на залишку
- скоротити час, що виділяється на роботу із замовленнями
- знизити партії замовлення і підвищити їх частоту, а отже, і прискорити оборотність запасу.
Також у будь-який момент в кілька кліків можна отримати відповідь на низку важливих запитань, що характеризують стан запасів у ланцюзі постачань:
- за якими позиціями утворився недостатній запас і чи розміщені замовлення на їх поповнення
- за якими SKU може настати прогнозований дефіцит, незважаючи на те, що є замовлення на поповнення
- яка динаміка роботи із зайвим запасом, чи знижуються overstock у кількісному і грошовому вираженні
- чи працюють менеджери за системою і який відсоток редагування замовлень
- чи вистачить сировини для запуску всіх необхідних завдань у виробництво
- у яких категоріях, на яких складах, у запасах яких постачальників або менеджерів зосереджений основний потенціал для вивільнення оборотних коштів.
Можливість моделювання сценаріїв
Система надає можливість промоделювати, як вплине на цільовий запас зміна логістичних параметрів. Наприклад, як зміниться середній залишок SKU, якщо вирішимо його поповнювати частіше / рідше, або перейдемо на постачання від іншого постачальника, у якого відрізняються умови, або замість керування за прогнозним типом споживання перейдемо на фактичні минулі продажі чи змішаний тип.
Завдяки цьому компанія мала змогу проаналізувати, який запас передбачається по конкретним позиціям за 2 схем постачань – з підтриманням залишку на Центральному складі та поповненням регіонів і при крос-докінгу (без зберігання запасу під регіони на Центральному складі).
З точки зору обсягу підтримуваного запасу і його структури, оптимальним виявився варіант зі зберіганням – оскільки передбачає коротше плече постачання, частіше замовлення, тобто можливість зберігати менше на залишку регіонів й оперативніше реагувати на мінливий попит на місцях завдяки наявному на Центральному складі загальному запасу.
Основні ефекти, які отримують міжнародні компанії від впровадження Intuiflow
Результати від роботи системи. Як Intuiflow працює в режимі суттєво вираженої сезонності?
Протягом останнього етапу впровадження системи, команді вдалося вийти за рамки операційного рівня управління виробничими запасами на тактичний, у площину середньострокового планування, за допомогою модуля Sales & Operations Planning. Цей модуль дає змогу моделювати обсяги постачань, виробництва, середній залишок на горизонті до 1,5 років.
Прикладне значення цього блоку суттєве, оскільки:
- можливо оцінити, який обсяг інвестицій у запаси знадобиться в майбутньому і скільки місця на складі ці запаси займатимуть
- можна побачити заздалегідь вірогідні майбутні дефіцити, до яких необхідно підготуватись
- є уявлення про те, який орієнтовний обсяг постачань буде отримано від контрагентів або буде випущено з виробництва. Можна надати постачальникам доступ до цих даних, для того, щоб вони могли слідкувати за змінами в потрібних обсягах відвантажень і підготуватися до них, підвищувати свій рівень надійності. А також виробництву, щоб останнє мало змогу планувати кількість людей і змін, яка знадобиться для виготовлення таких обсягів.
Останній етап впровадження припав на завершення сезону активних продажів. Були змінені системні налаштування, і вихід із сезону було здійснено за допомогою коефіцієнтів сезонності PAF (Planned Adjustment Factor).
Оскільки в продажах присутня чітко виражена сезонність, а виробничі потужності обмежені, доцільно заздалегідь готуватися до сплеску продажів, рівномірно навантажувати виробництво, перенести випуск сезонного обсягу продукції на місяці, що передують настанню буму продажів. Для рівномірного і своєчасного нарощування обсягів, що випускаються, було використано інструмент CDAF (Cycle Day Adjustment Factor).
Висновки
Усі ці результати стали можливими завдяки щоденній наполегливій роботі всієї команди, прагненню глибоко розібратися в принципах методології DDMRP і застосувати їх на практиці. Цей процес демонструє, наскільки важливо інтегрувати інновації в управлінські підходи, оскільки вони відкривають нові можливості для покращення ефективності, оптимізації ресурсів та підвищення конкурентоспроможності компанії.