Cloud inventory management at Monomakh Tea Production: Achieving a 59% Sales Boost
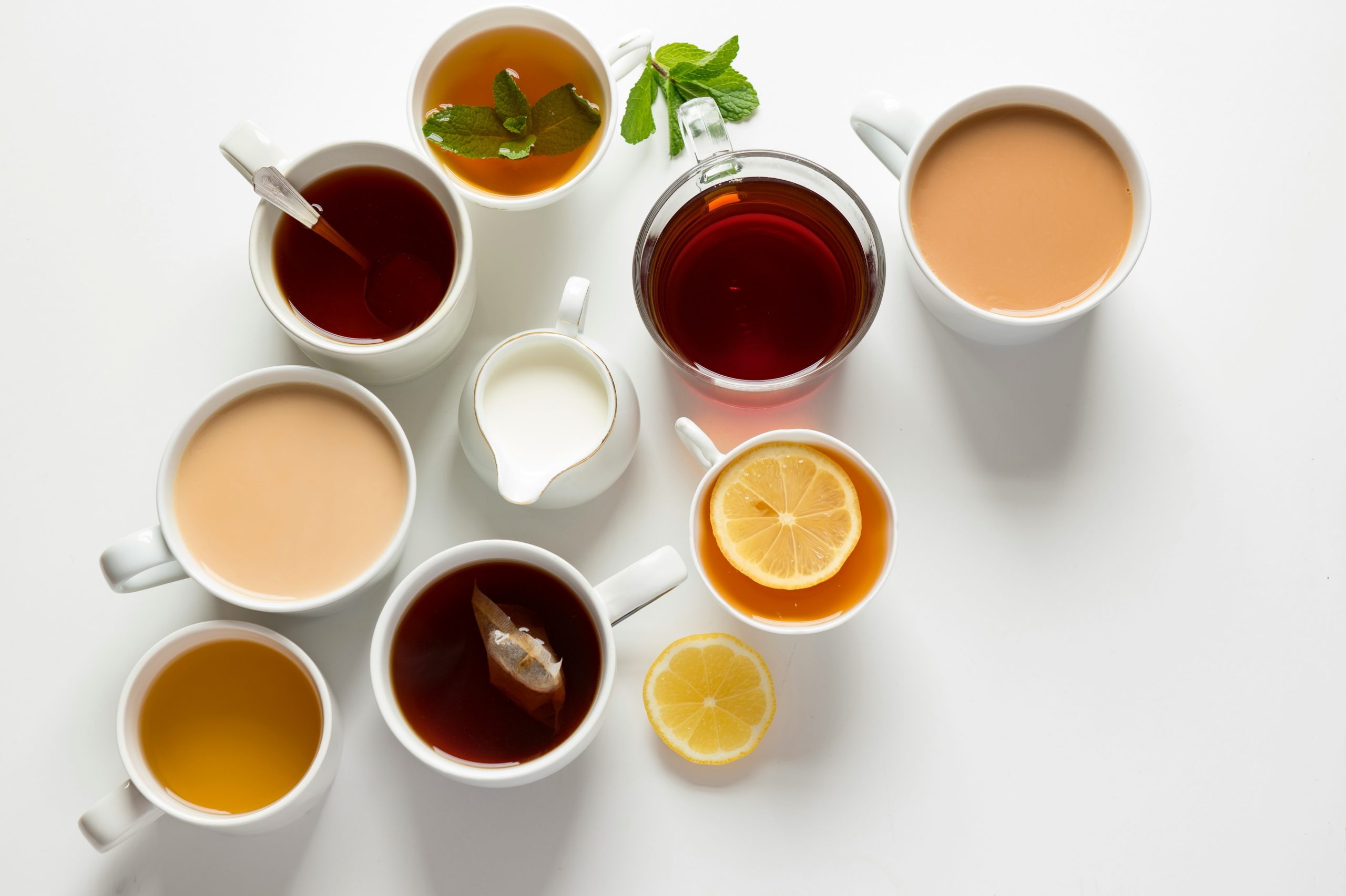
In this article, we will look at what business specifics led Monomakh to search for new solutions to automate the production of coffee and tea. Namely, to find a tool for cloud inventory management.
About Monomakh, production company
Monomakh is the №1 tea and coffee company in Ukraine. At the initial stages of its operations, the company imported packaged tea from other countries, and later switched to importing bulk raw materials. Today it is a modern production, processing and packaging facility of tea and coffee.
Some facts about Monomakh:
- The company produces 10 thousand tons of products annually
- Product quality is controlled at every stage of production
- The company has 250 positions of its own brand
- Together with own brands – 1500 items of tea and coffee
- Raw materials are supplied to the factory from certified companies
- 75 companies trust the packaging of their products to VTM, such as: Unilever, Strauss Ukraine, S.G. Production, ATB, METRO, Fozzy Group, Auchan, Novus.
Difficulties in inventory management:
Monomakh invited INTUIFLOW team experts to their production facility to audit the inventory management system and review current supply chain management processes.
The survey revealed the following strengths of the production organization
- multi-level product quality control
- modern packaging technologies
- high level of production capacity
It also highlighted the difficulties in inventory management:
- Raw materials shortages
- Semi-automatic ordering process
- Managing a long list of SKUs in Excel spreadsheets
- Lack of control over order fulfillment by raw material suppliers
- Lack of reactive analysis of changes in inventory levels
- Lack of a centralized data management system
Pre-project goals of Monomakh:
- Ensuring the availability of the necessary products to meet incoming demand
- Efficient inventory management along the supply chain
- To Reduce raw materials and finished goods inventory
TOP 3 features of the tea business in Ukraine that affect effective inventory management
Ukraine is not a tea or coffee-producing country.
They are a fully imported raw material, so the lead time is 3-3.5 months.
Seasonality of sales.
This is due to an increasing consumption of hot drinks in the fall and winter, and a decreasing consumption in the spring and summer.
Seasonality of purchases.
There are certain months of the year when it is much more profitable to buy raw materials. It depends on the harvest and the exchange rate.
The Monomakh management realized that the company lacked a specific tool that could cope with the peculiarities of the business to effectively manage its inventory.
Why did Monomakh choose cloud inventory management?
INTUIFLOW is significantly different from other systems due to its unique Demand Driven MRP (material requirements planning based on real demand) inventory management methodology. This methodology has incorporated the best practices of production and supply chain organization – TOC, Lean, 6 Sigma, DRP, MRP and a significant block of innovations. The key effects of implementing this methodology include a reduction in inventory of up to 40%, sales growth of 20% and an increase in the service level.
When getting acquainted with the INTUIFLOW methodology and SaaS solution, an important role was played by the fact that Monomakh employees drew attention to the results of system implementation in such companies as: Kormotech, Coca-Cola Beverages Africa, Michelin.
Average results of INTUIFLOW SaaS implementation in the FMCG industry:
- Reduction of inventory by 50%
- Increase in Service Level by 20%
- Reduction of Lead-time by 45%
After all these reasons, Monomakh’s management made a decision to implement INTUIFLOW, the cloud inventory management system (INTUIFLOW).
Training course:
The implementation process was accompanied by user training at all stages:
- The training seminar is a comprehensive DDMRP inventory management methodology course.
- LMS, Providing video tutorials showing how to work with the algorithms and settings of the program.
- Employee training on the system’s reporting and analytics
Volodymyr Ropalo (Deputy General Director for Production Logistics) noted the training phase was quite fast, and after 2-3 weeks, his team was able to fully work with the cloud inventory management software.
What are the results of Monomakh’s cloud inventory management?
Monomakh has implemented the SaaS solution – INTUIFLOW. At the moment, 100% of the entire active inventory is under the control of the system. The following results were achieved in 2 years (check the graph below):
First year:
- Sales growth of 30%
- Inventory growth by 27%.
Second year:
- Sales growth of 59%
- Inventory growth by 2%

- Purchase order process created
- Automated orders to suppliers and production
Today, ABM Cloud’s Customer Success team continues to communicate with Monomakh’s team, providing support and assistance on all issues. Due to the Intuiflow evolution, version updates are seamless and do not require the participation of the client.
Monomakh managed to achieve key results in effective inventory management due to the fact that the entire team of professionals was interested and involved in the implementation process.

The DDMRP methodology has greatly simplified inventory management. This was possible thanks to a team of like-minded people who are not afraid of change. Now there are no Excel spreadsheets, only data taken from the INTUIFLOW.
Volodymyr Ropalo, Deputy General Director for Production Logistics.